Hydraulic Hot Forging Press for Automobile Shock Absorber ShellUpdate:2023-05-03 Hits:127
Shock absorber is one of the key components of the car, and its working performance is directly related to the safety and comfort of the car. Hydraulic shock absorbers are widely used in the automotive industry because of their good damping adjustability. However, the manufacturing process of the shell of the hydraulic shock absorber is relatively complicated, and the welded structure has always been used, and the weld seam is easy to crack during use. The shock absorber shell is integrally formed by hot forging, which avoids the use of welding technology and improves production efficiency. Hot extruded aluminum alloy automobile shock absorber shell, can choose four-column hydraulic hot forging presses or frame hot forging presses.Hot forging of automobile shock absorber shell requires comprehensive analysis of process parameters such as extrusion material, extrusion speed, lubrication, billet, and mold heating. Extrusion is to install the extrusion die on the press, and use the reciprocating operation of the press to make the metal plastically deformed under the three-dimensional compressive stress at a certain temperature, thereby extruding parts of the required size, shape and performance.
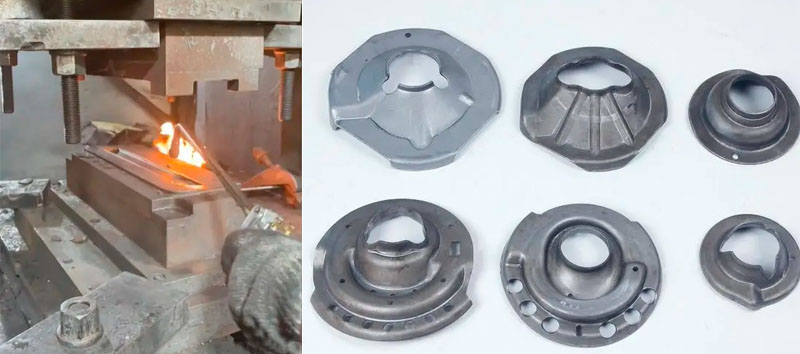
The invention discloses an aluminum alloy production process for automobile shock absorbers, belonging to the technical field of Al-Zn-Mg-Cu series aluminum alloy materials. It first melts and casts aluminum ingots, and homogenizes the melted aluminum ingots; heats the aluminum ingots to 470~500°C, and uses a hydraulic hot forging press for positive aluminum alloy automobile shock absorber shell, to extrude, and the extruded products are processed online Spray water for cooling; straighten sawing after cooling, and finally perform artificial aging heat treatment on the sawn products. The 7003 aluminum alloy production process for automobile shock absorbers can not only produce high-strength and high-elongation automobile shock absorber products, but also improve the surface quality to meet the actual use of automobile products.
Preparations for selecting a suitable hydraulic hot forging press for aluminum alloy automobile shock absorber shell :
1. Draw up extrusion drawing
2. Select the molding process plan
3. Determine the size and shape of the blank;
4. Draft the extrusion process;
5. Calculate the extrusion force;
6. Select hydraulic press equipment.
Delishi/Goodsjack Hydraulic Machinery recommends hydraulic hot forging press for aluminum alloy automobile shock absorber shell to choose 1250 tons, 1500 tons, and 2000 tons. Four-column structure hydraulic presses can be selected, and frame-type hydraulic presses can also be selected according to needs. The four-column structure is simple, economical and practical; frame The structure has good rigidity, high precision, strong anti-eccentric load capacity, high precision of hot extrusion, and reduced machining allowance. The electrical system adopts mature PLC control, which can ensure the safety of equipment and operators. A reliable cooling circulation system is installed, which can stably control the temperature rise and ensure the safe and reliable operation of the system. Servo motor direct drive, simple structure, low maintenance cost; small vibration and noise, will not disturb the people, meet the requirements of environmental protection; when approaching the bottom dead center, the slider speed is extremely fast, the time for the mold to extrude the material is very short, extending the die life.